chassis torsion test|CHASSIS TORSIONAL RIGIDITY: VALIDATION OF FEA : trader The test stand consisted of a lever arm rigidly attached to the front axle, which constrained it from rotation about the axle, in order to apply a torque to simulate suspension loading. The rear axle was fixed in all three degrees of translational freedom and two degrees of rotational freedom. webInstagram Password Finder - The Best website to Hack Instagram account instantly with ease - Best Instagram Password Hacker / Cracker tool
{plog:ftitle_list}
Resultado da 1 de jul. de 2023 · Para conseguir esta forma, o Saiyajin precisa da ajuda de mais 5 seres da mesma raça e todos precisam ter um bom coração para transferir seus poderes e sentimentos para ele. Com essa transformação, o cabelo do usuário ganha a cor vermelha e sua aura de luta e olhos .
This model examines the frame and overall chassis torsional stiffness relative to the suspension spring and anti-roll bar rates. A finite element model is next developed to enable the analysis of different frame concepts.We simulate and physically test our chassis torsional rigidity by the textbook method of securing the rear and applying a weight to a lever arm secured to the front suspension, all done with solid links.Because of this, torsional stiffness affects the vehicle’s performance and behaviour significantly [1,2]. Teams evaluate the torsional stiffness of the frame to determine the design’s quality and find out whether the frame is rigid enough compared to the roll stiffness of the suspension.The test stand consisted of a lever arm rigidly attached to the front axle, which constrained it from rotation about the axle, in order to apply a torque to simulate suspension loading. The rear axle was fixed in all three degrees of translational freedom and two degrees of rotational freedom.
The design of a torsion spring has been formulated, but it is difficult to determine the local behaviors of torsion springs according to actual load conditions. This study proposes a torsion-spring design method through finite element .Once there is the chassis projected and constructed, is important to verify the math models and determine exactly what characteristics the structure has achieve in terms of torsional rigidity.
In this video, you will learn how to apply loads & boundary conditions on chassis models and solve for stress and deformation. Torsion and cornering test wil.The team FGR UnB provides his chassis for the test with two different types of clamping to observe its consequences. . which is the event that provides the torsion on chassis. Figure 8: Model 1 .
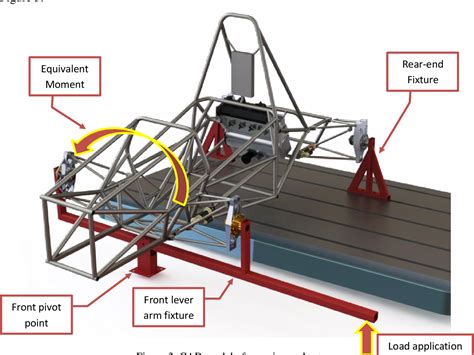
Just researching options for doing physical torsion testing for the chassis and basically from what I've read so far come up with basically making plates to lock the two rear hubs to the ground and the front left wheel while resting the chassis at the centre of the front axle on a pivot and loading weights onto the front right hub followed by taking readings from the dial gauge on the . This paper reviews three different approaches to determine the torsion stiffness of an automotive chassis and presents a Finite Element Analysis based method to estimate a vehicle's torsion stiffness.Stress-Relaxation Torsion Test: This test measures how torsional stress decreases over time at a constant strain, relevant in applications where long-term stress relaxation is a concern. Creep Torsion Test: In this method, a constant torsional load is applied for an extended period to observe how the material deforms over time, known as creep.
We simulate and physically test our chassis torsional rigidity by the textbook method of securing the rear and applying a weight to a lever arm secured to the front suspension, all done with solid links. Everything I've seen and read about testing torsional rigidity uses this method, but some of the judges is design gave us a ton of flak for this.Figure 1: Schematic showing torsion in chassis.3 The first step in any engineering problem is to break it down into its simplest form and fit it to a theoretical model. Torsion, in its simplest form, is defined on a solid circular member (depicted in Figure 2). From Mechanics of Materials (or Solid Mechanics), the applied torque couple, TVSB14 Chassis Torsion & Beaming. Torsional and beaming stiffness are key indicators of a chassis’ structural integrity and any individually constructed vehicle (ICV) must meet torsion and beaming requirements under VSB14 guidelines. BremarAutomotion can conduct virtual torsion and beaming using FEA modelling based on CAD models of your .
Torsion Rig The torsion rig used to test the chassis and illustrated in Fig. 3 is a steel welded frame, constructed mainly from standard sections, with a limited number of specially machined .FULL CHASSIS TORSION TEST A better way to assess the structures capabilities is to twist test the entire chassis assembly. There are a variety of methods to load a chassis in torsion. One of these methods is discussed in [1]. This method involves constructing a fixture with two jacks at the front of the car, and two fixed supports at the rear.

An example for a torsion hydraulic actuator test (Figure 2.1) for the medium velocity range is given by Lindholm and Johnson [2], cited in the ASM Handbook vol. 8 by Lindholm et al. [3], with the determination of shear-stress–shear-strain curves of different materials.The failure strain and the strain-hardening coefficient are taken. The specimen used was a tube form with an outer .
In addition to a torsion test, local and whole-chassis FEA can show performance for different chassis designs during combined cornering, aero and bump loads, for drivetrain attachments during acceleration and braking, and for harness and other mounts during front impact. . Minimal torsion test constraints at rear damper / rocker mounts: Fixed . A vehicle with high torsion rigidity will give the driver and passenger a more “solid” feel when the car is running, especially when the road is bumpy and has lots of potholes on it. . 16,440 (actual test), 21,667 (CAE simulation) Link Honda Accord Sedan (2013 – 2017, 9th-Gen) 23,345 Honda Accord Sedan (2018 – , 10th-Gen) 37,700 Honda . In this work, the effects of overall chassis flexibility on roll stiffness will be determined using a finite element model (FEM) of a Formula Student Chassis and suspension. The Validation of the model is done by designing and fabricating a test rig to experimentally determine the Torsional Stiffness.
Development of a Test Stand for Determining the Torsional
Part 2 | FSAE Chassis Side Impact Simulation in SolidWorks | FSAE Chassis Torsional Simulation in SolidWorks | Formula Bharat Chassis | Formula Imperial Chas.
There’s no point hiding the love for the new Land Rover Defender, we here at Car Journalism have been a fan right from the start. Even bigger fans after driving the 90 derivations and we’ve become groupie-like when the V8 .DOI: 10.1016/j.matpr.2022.01.019 Corpus ID: 246088509; Torsion test for a BAJA chassis using gyroscopic sensor and validation of CAE results @article{Jindal2022TorsionTF, title={Torsion test for a BAJA chassis using gyroscopic sensor and validation of CAE results}, author={Rohan Jindal and Rishabh Arora and Rishabh Papney and Manan Patel and Rakesh Chander Saini .A comparison of frames tested in isolation versus whole vehicle testing is made, and a simple whole-car chassis torsion test method is discussed. INTRODUCTION This paper examines several aspects of vehicular frame design, with an emphasis on application to an open- Figure 1: Longitudinal Torsion Deformation Mode wheeled, space-frame racecar .
Next a simple spring model is developed to determine targets for frame and overall chassis stiffness. This model examines the frame and overall chassis torsional stiffness relative to the suspension spring and anti-roll bar rates. A finite element model is next developed to enable the analysis of different frame concepts.
This paper will provide you an easy way to understand and then perform the torsion test of the vehicle chassis [8], [9]. The longitudinal torsional stiffness is the key property of a vehicle’s frame. It means the resistance offered to torsion along the longitudinal axis while cornering or as a wheel travels over a bump. If the frame does not .Chassis is the base frame of any vehicle that provides the structural support and rigidity to it. . go-kart might encounter that will test its structural rigidity, a series of analysis were done using FMEA, including Impact . tested whether the chassis will be able to withstand torsion impact. Analysis of the designed chassis was obtained usingOur solution was to support the chassis at three points, and add sandbas to the 4th, and measure the deflection along each rail. Then repeat with the chassis flipped round, to test the rear. This of course mixes torsion and bending, but the FEA could then be used to examine how much of the deflection was due to each. Estimate mass and simulate a torsion test for each design iteration. Try adding or subtracting tubes. . When the accumulator mounts stick out from the imaginary box around the cells, use gussets to brace against the test load normal to the mount. If the chassis mounts are not directly through a welded insert into the tube, use gussets along .
and experimental works of a test apparatus for chassis testing of a formula student car. The apparatus is a solid jig with an . Torsion loads result from applied loads acting on one or two .I'm surprised at the lack of actual chassis torsion tests here - everyone seems to be doing full compliance tests. While it's good to know how much (or little) your corner assemblies add to overall rigidity, an industry standard torsion test does not include any suspension components. This is why you see new and updated sports cars come out .
I've done a torsion test on a car chassis with one end secured and the other end attached to a device which has a bar connected perpendicular to the chassis which rests on an arced section of steel on the floor. Now the arced section was placed centrally to the chassis and a load applied on the end of the bar.
Request PDF | Torsion test for a BAJA chassis using gyroscopic sensor and validation of CAE results | Vehicle dynamics plays an important role in vehicle stability, handling, ride quality and control.
Design, Analysis and Testing of a Formula SAE Car Chassis
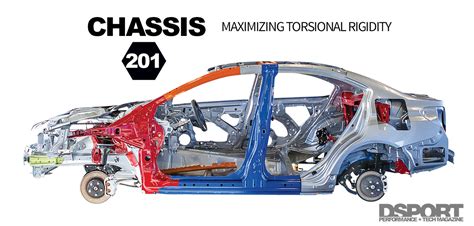
Resultado da Confira avaliações e notas de clientes para Makita XT801X1 18V LXT Íon-lítio sem fio, 8 peças (3,0Ah) na Amazon.com.br. Leia avaliações reais e imparciais de nossos usuários sobre os produtos.
chassis torsion test|CHASSIS TORSIONAL RIGIDITY: VALIDATION OF FEA